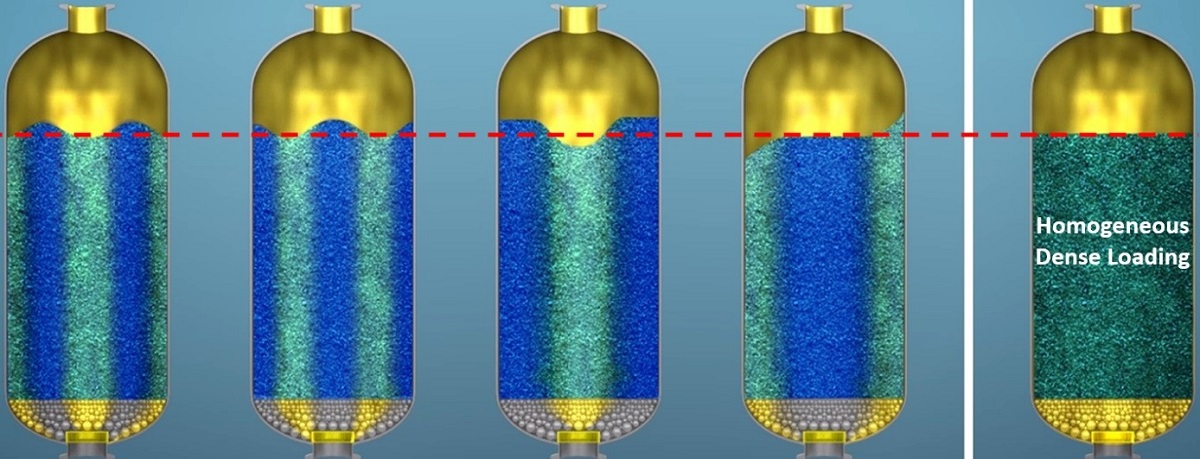
Published by CREALYST the 22/11/2018
What impact does catalyst packing have on unit performance? PTQ Catalysis Q&A March 2018
Thiago CALDAS, Dense loading expert Crealyst-Oil & Guillaume POUSSIN, R&D Manager, Crealyst-Group answered to this strategic question in PTQ Catalysis Q&A March 2018
The specific performances of a process unit are directly linked to catalyst packing or its internal distribution. Poor catalyst organization inside the reactor means lack of homogeneity, which generates different oppositions to the passage of the fluids and this is the origin of pressure drop gradient. Generally, dense loading service is the most obvious answer for a good catalyst distribution.
Nevertheless, three main issues have to be satisfied together while operating dense loading:
1/ getting a real homogeneous dense loading in all directions,
2/ keeping a fast and safe loading,
3/ protecting the catalyst particles integrity during loading.
For the first point, some loading operations are satisfactory in terms of average density but unsuitable in terms of local gradients like, for instance, radial pressure drop homogeneity inside fixed-bed reactors (Figure 1 and 2 below), or non-flat bed surface during loading.
In these examples, hydrocarbons flow easily into lower density regions, forming preferential ways. Through these channels, the flowrate of fluids is greater than in other parts of the reactor and, consequently, the intensity of coke formation increases.
The result is the formation of hot spots and critical adverse effects in the reactor efficiency by loss of yields.
To preserve the process from such difficulty, the quality of dense loading is essential: the catalyst particles need to be as isolated as possible to drop freely (Figure 3 below).
Very precise control of the particle trajectories is expected by uniform control of the distribution “by zone”, taking great care of the catalyst particles to avoid attrition or degradation.
Crealyst-Oil has improved Calydens® equipment since its creation in 2004, in order to reach total flatness of catalyst beds and full homogeneity.
Experienced specialists are thoroughly trained and nine different versions of the machine have been developed since in order to adapt specific solutions in terms of Homogeneous Dense Loading®.
Calydens® is able to realize a controlled and regular introduction of catalyst by producing a rain effect, and is the only machine able to cover all the diameters of any reactor even if the bed is really close, up to 300 mm, from the distribution tray.
The direct impact of the homogeneous dense loading is to load more catalyst (15- 25% more catalyst in the same volume).
The main impacts of the homogeneity effect on unit performances are lower operating temperature, lack of hot spots inside the catalyst, stable radial temperature, higher yields and longer cycle of operation, without channeling, and total catalyst used equally.